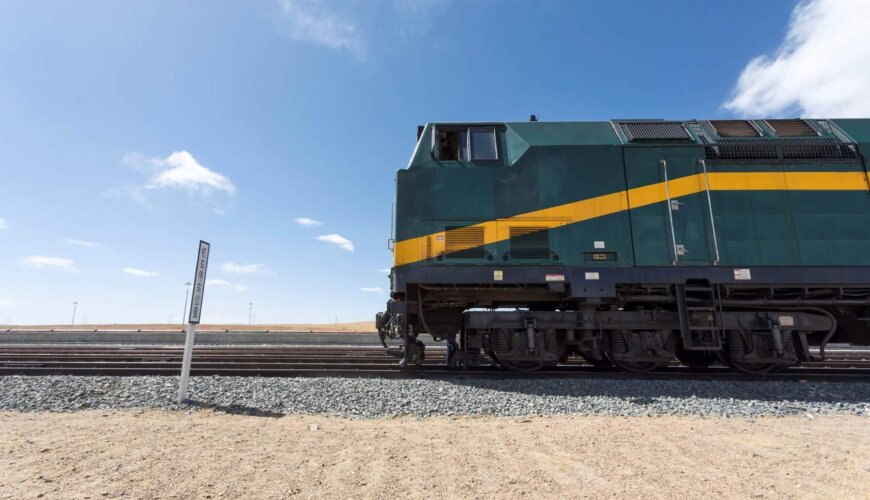
Three reasons to weigh a moving train
Weighing is a routine task in rail transport, as it determines whether the vehicle is meeting safety standards in order to travel, considering the impact that excess weight can have on the life of the rails and wheels.
Furthermore, weighing can reduce costs when used in situations opposite to the one mentioned above. Transporting requires a cost of labor, repairs, fuel, and therefore it is not worth it to put a train in motion to transport less than its capacity.
There are different types of weighing, with different systems, and each one has specific characteristics that are crucial for engineers who design a railroad transport system.
The most common in the rail transport market are the flow scale, static scale, batch scale and, finally, the scale that is the subject of this article, the dynamic scale. Next, we'll delve into the 3 reasons for weighing a moving train, including a bonus reason.
Content Index
Optimization of the weighing process
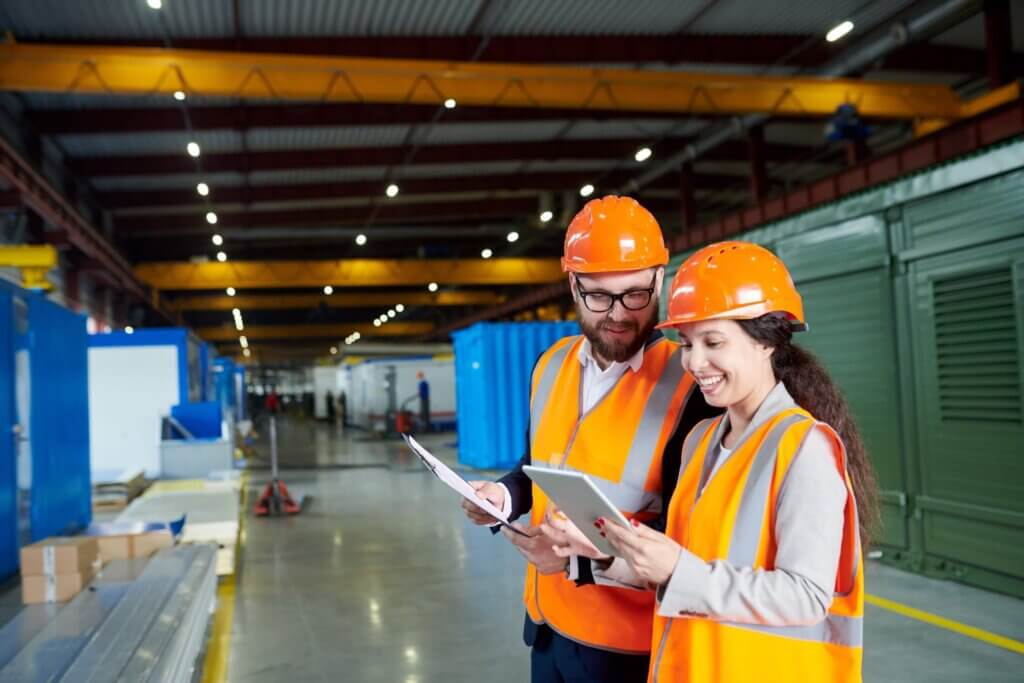
In the transport sector, be it road or rail, one of the priorities is the speed with which such transport is carried out. Therefore, investment in technologies and strategies to reduce the time a machine travels long distances has grown and generated great results.
All processes that precede transport are designed for efficiency and speed, from maintenance to the weighing of the wagons.
Before, to preserve the condition of the wagons and ensure that they did not pose a risk, each one of them was statically weighed. This weighing consisted of uncoupling the assembly and weighing each of its parts individually.
Despite the accuracy, static weighing involved a lot of time to be done and processed accurately, which comes at a high cost for an industry that is known for speed.
For this reason, and thinking of a solution, the dynamic scale was developed, which can weigh the train in motion and guarantee the optimization of the logistical processes involving railroad transport.
A dynamic scale can weigh the set with a speed of up to 10Km/h, with an efficiency of up to 99.8% when weighing a wagon. Another feature is its flexibility, which allows for individual wagon weighing, individual train weighing, axle weight weighing, truck weighing and weighing by distribution of loads per quadrant.
Safety
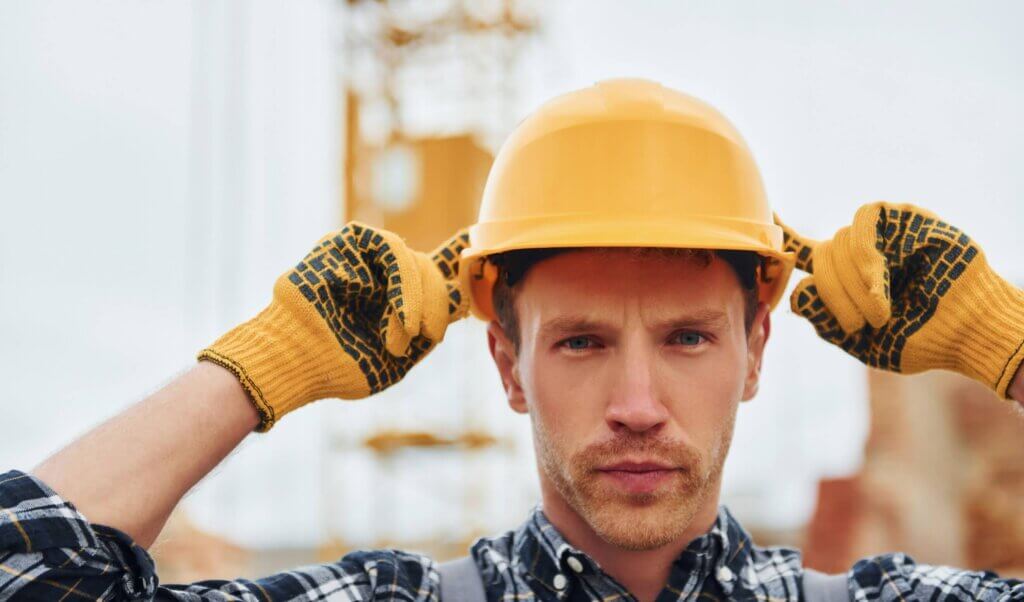
To ensure the safety of operators, maintainers and other professionals involved in rail transport, trains must operate in accordance with safety standards and meet technical specifications to ensure control of their operation.
Therefore, the weight with which these powerful machines operate is a factor that must be considered, given their durability, the quality of their parts and the risks that a malfunction can pose to operators.
The advantage of dynamic weighing, that is, with a moving train, is that there is no need to include operators in the activity, which allows maintenance without NR33, the standard that regulates confined spaces and requires a series of measures to protect the worker which performs repairs, maintenance and other activities.
If a moving train with no load is already heavy and causes wear on the rails and wheels, with excessive load or overweight,, it can shorten its useful life in an unforeseen manner, which can be even worse.
It is essential that the maintenance of this machinery can measure your physical capacity.If the tracks start to deform before the forecast stipulated by their manufacturers, it is up to the maintainers to find these faults and intervene before accidents can happen.
For this type of situation that dynamic scales are designed for, calculate the weight of the wagons and their assembly before they can result in excessive wear, shortened service life and accidents.
Fuel Saving
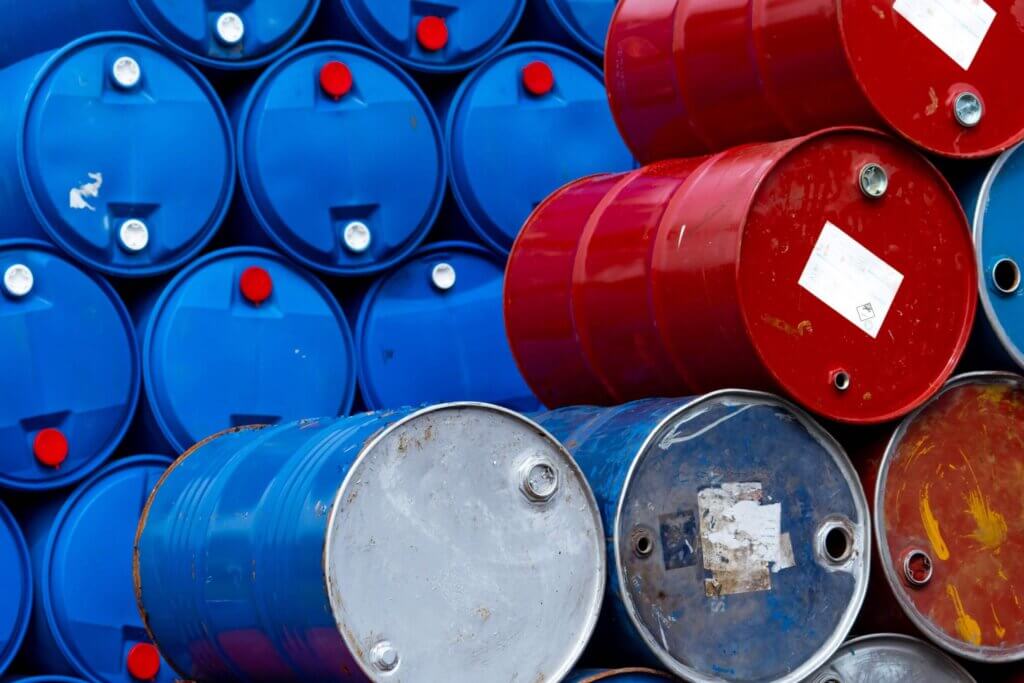
The amount of fuel a train needs to travel is large, due to its weight. Therefore, all processes involving its circulation are planned to the point of reducing costs and optimizing its performance.
This means that the less fuel used for this machine to operate, the better. Static weighing a train does not only imply stopping it, but also maneuvering it.
It may not seem like it, but because they are routine procedures, weighing happen very often and, in the case of static, they demand more fuel due to the maneuvers.
Investing in a weighing system that operates with the train in motion not only generates savings by avoiding being overweight, but also by not needing to maneuver to points where the cars are uncoupled and to the weighing locations.
BONUS REASON: Decrease in the number of operators
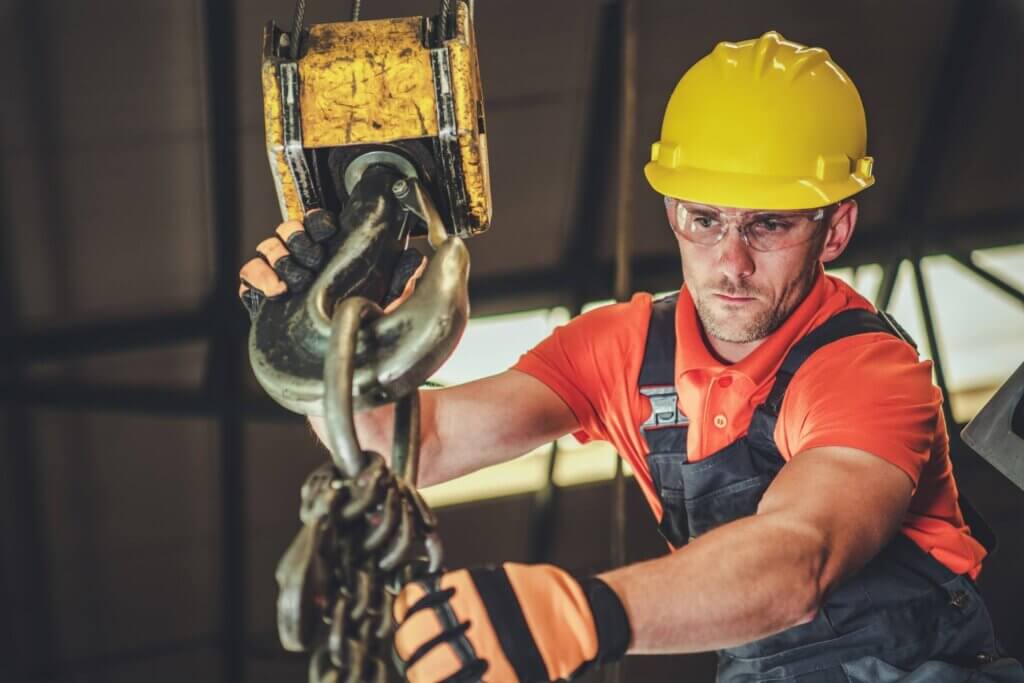
As we mentioned earlier, dynamic weighing does not require many operators to perform.
Even though they are still needed, the workers have a reduced task demand compared to weighing. As there is no safety in carrying it out with employees inside the moving train, the process is done with the cars connected.
For dynamic weighing, MASSA uses the SIMMSOFT software, which has the ability to weigh the train in motion, with all its parts and even isolate them efficiently, rejecting any human intervention to differentiate wagons with different loads, or as a whole.
Conclusion about the weigh a moving train
So far, we have differentiated static weighing from dynamic weighing and the benefits of the latter.
Designed to improve the efficiency of rail transport, dynamic weighing optimizes logistics, as it facilitates work without the parts that make up the train having to be disassembled.
In places where train locomotion is high, there is no time to stop trains and maneuver them one by one with separate carriages.
In addition to dynamism, this tool can reduce costs related to the use of fuel, for all stops and labor, often required to uncouple and couple the cars before they can circulate again.
Searchs:
https://www.mrs.com.br/post-blog-inovacao/balanca-ferroviaria-dinamica/
https://www.mt.com/br/pt/home/products/Transport_and_Logistics_Solutions/rail_scales.html