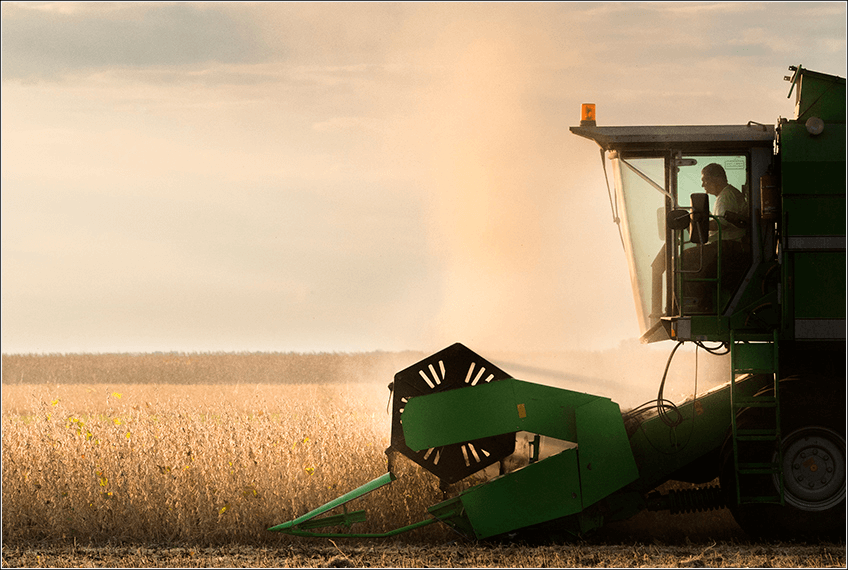
Grain Hopper: 5 Biggest Challenges!
Agribusiness production continues at full speed, and grows every year. However, there are still some challenges that need to be overcome, such as storing inputs in the grain hopper.
In case you didn't know, the grain hopper is a structure used to receive the grains harvested in agribusiness, acting directly in the storage and supply of cargo transport vehicles, especially trains.
O hoppers work as follows:the trucks are positioned on these structures and elevated, with this, the loads present in the anterior parts of the compartments of these vehicles fall, passing through grates, reaching the conveyor belts, which carry these grains to the storage locations.
For these structures to become increasingly well used, it is important that companies involved in unloading and loading grain into transport vehicles know how to identify the main problems and how to overcome them.
Therefore, we selected the 5 biggest challenges for the grain hopper to be better used.
Content Index
Dirt from the grain hopper
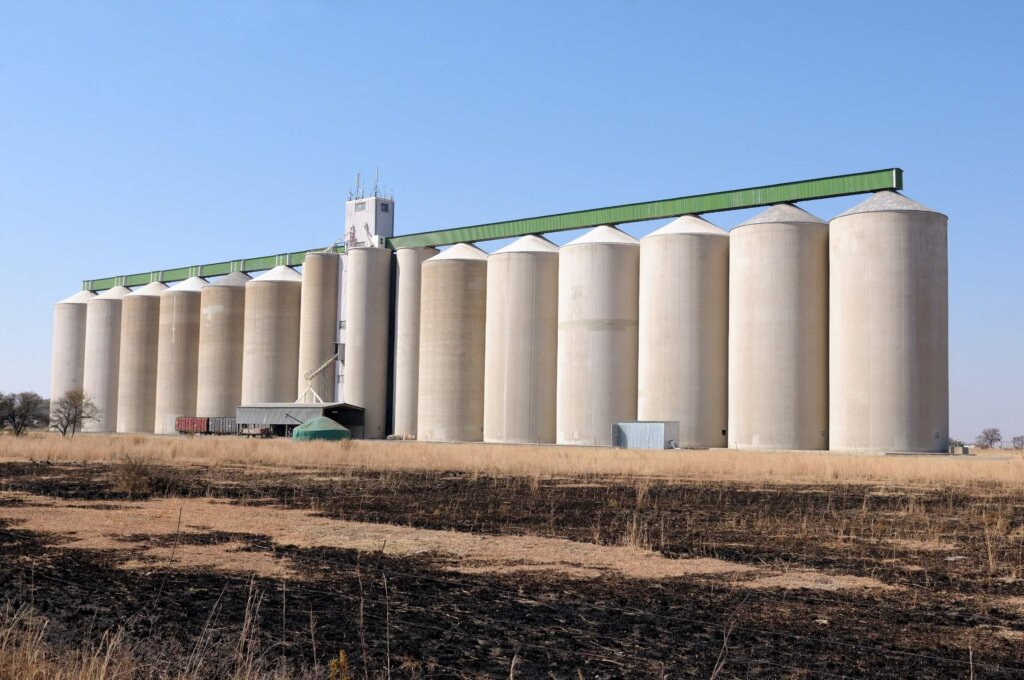
This process of supplying the grains in the hoppers, and later from the hoppers to the vehicles, takes place all the time. As a result, it is common for the grains to be stuck to the hopper structures, causing several elements, especially the grids, to become dirty, which is one of the main errors in weighing freight cars..
As hoppers are essential for companies to be able to weigh the grains, determining the final weighing of train cars and the complete composition of a railroad vehicle, it is essential that this process is performed as well as possible.
As the grain hopper remains dirty, with elements from other batches of grain attached to the grids and other compositions, this directly interferes with the weighing of the bulk wagons.
Many of the wagon weighing take place on static scales, right under the railroad hoppers. In this sense, this interference can be decisive for incorrect weighing, which can cause damage to the sectors involved and stop the processes.
Furthermore, this can affect the quality of the grains that will be deposited in vehicles. If a consignment is contaminated, for example, and gets stuck in the hopper structures, a whole new batch can be harmed.
Therefore, one of the main challenges in using the grain hopper is to be able to properly clean the railroad hoppers after filling a batch of grain.
It is a difficult challenge to be faced, mainly due to the incessant routine of the stations where the hoppers are present. Often, the time between filling one wagon and another is very short, making it difficult to carry out this cleaning efficiently.
Waste
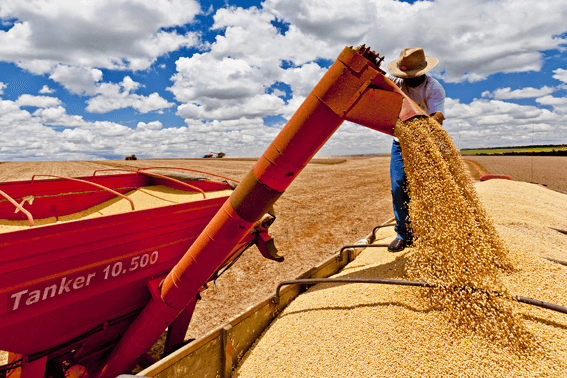
Widespread waste is one of the main problems faced by agribusiness. In relation to food inputs, such as grains, for example, it is estimated that, only in production, 10% is lost in the field, while 50% of the losses occur in transport.
The use of the grain hopper is part of this production chain, and it is essential for the harvested grain to be stored and deposited in vehicles, whether trucks or trains.
In this process, the grains can be wasted by the hoppers, especially when weighing vehicles on static scales..
As the trains have to stop to be supplied by the railroad hoppers and weighed in this model of scale, unfortunately this is still a deficient process, which causes a series of waste, for various reasons, such as the retention of grains in the hoppers' grids.
Therefore, this is another challenge that must be overcome. Avoiding the waste of grains in this production chain is essential for agribusiness companies to be able to increase their profitability and collection of resources.
If grains continue to be wasted as they are today, it will certainly be difficult to improve this growth.
Accident risk
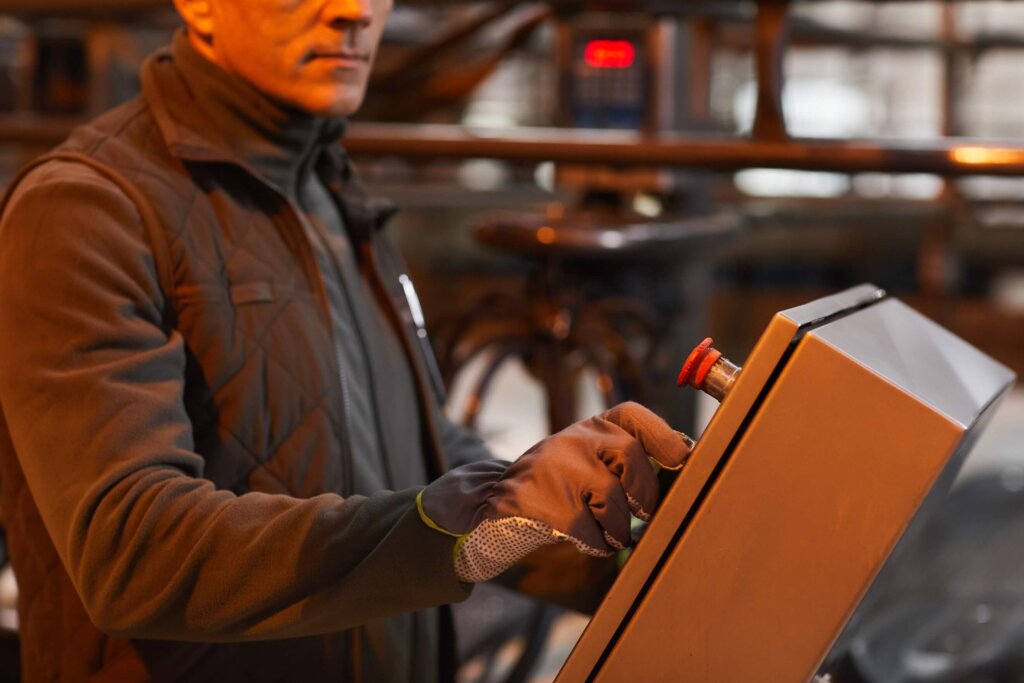
Because of the way they are built, in closed, stuffy and cloistered environments, hoppers are considered dangerous spaces, especially if the work of professionals is not well planned and executed.
The way the hopper is built influences the creation of environments like this inside the grain hopper. Many times, hoppers are built in underground spaces, which further provides this possibility for the environment to be small, dark, closed and enclosed.
In this way, there is a certain risk for the work of professionals who work in the hoppers, in terms of cleaning, supply and maintenance.
The main types of accidents that can occur in environments like this are the explosion of particulate materials, engulfment and burial.
Preventing these types of accidents from occurring is one of the main challenges in using the grain hopper, since, in addition to causing serious problems for the health and lives of professionals working in these environments, it can also cause a series of losses, both in terms of financial, as in the situation of the processes of the hoppers.
Underground moat creation
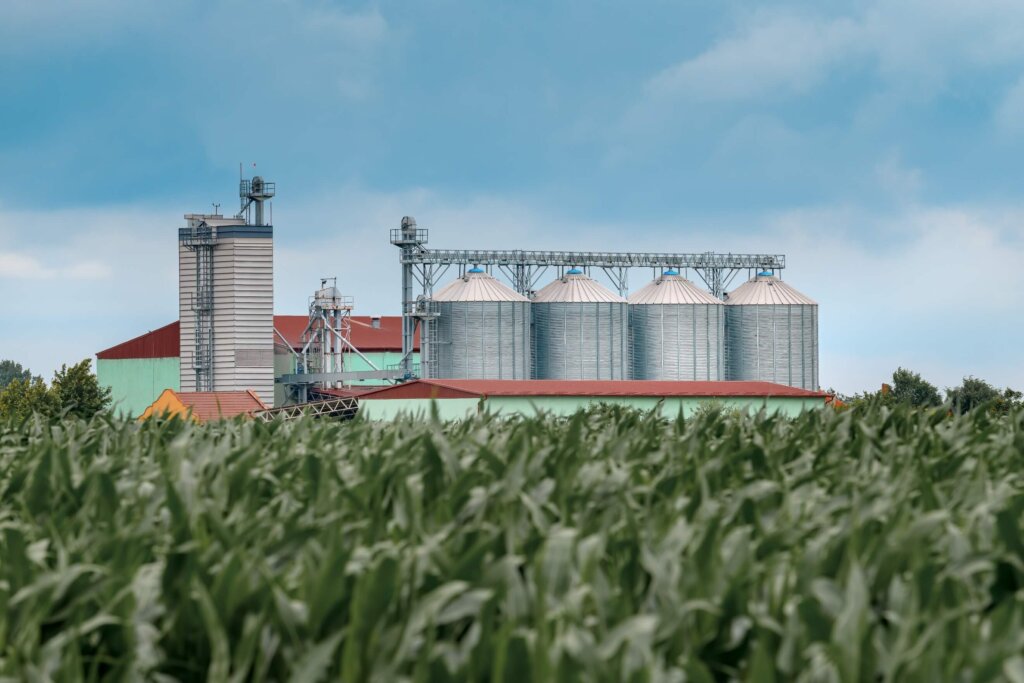
Taking the hook, as we mentioned earlier that many hoppers are built in underground spaces, which, in most cases, provides a more efficient process of receiving and supplying grain, it is important to highlight that there is a difficulty in improving practices in this regard.
For an underground hopper to function properly, it is essential that a grain hopper pit is built, which needs to follow all regulations stipulated for this type of construction.
The problem is that many companies still have difficulties in building hopper pits below ground level that are efficient and help in loading grain, whether in vehicles or in silos.
Therefore, it is important that companies understand how this process works. If you are facing difficulties in the construction of a qualified gap, it is interesting to count on the help of specialized companies, who know exactly how to implement this type of composition.
Dust Emission
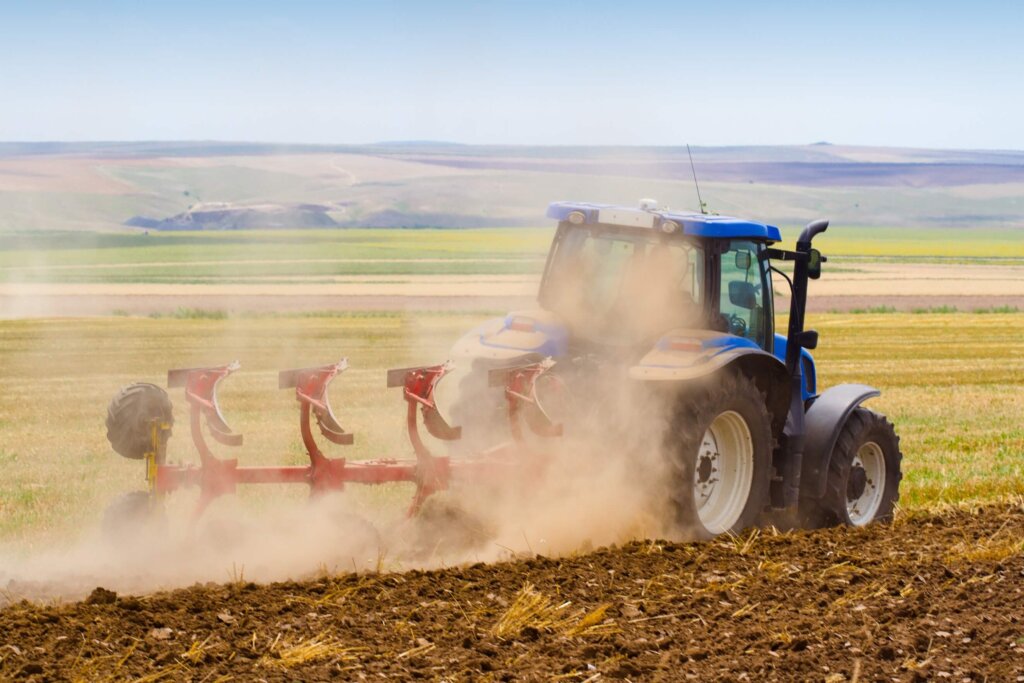
Another problem faced by the use of hoppers is the strong emission of dust that occurs during the processes of supply, storage and deposit of grain in rail and road vehicles.
This problem directly affects a number of people, not only workers who work in these spaces, but also nearby environments, people who circulate in the surroundings, among others.
The strong emission of dust can generate a series of health complications for these people, especially severe respiratory and pulmonary problems.
Therefore, this is another important challenge that companies that work with hoppers need to overcome, finding solutions that can reduce the emission of dust during the hopper processes, ensuring greater safety for the professionals involved in this work.
Conclusion: Grain hopper
As we have seen, the grain hopper is an extremely important structure for receiving grain, storing it and depositing it in transport vehicles. The problem is that there are still certain problems that need to be faced in order to improve the quality of these processes, ensuring greater productivity, correct grain weighing, improving the quality of life of people who work in these spaces and reducing grain losses and losses financially.
Searchs: https://massa.ind.br/vagoes-de-carga/
http://repositorio.roca.utfpr.edu.br/jspui/bitstream/1/5786/1/PB_CEEST_V_2014_07.pdf
https://pt.linkedin.com/pulse/estruturas-para-armazenagem-de-gr%C3%A3os-granel-julliano-macedo